2023 has been a challenging year for aquafeed manufacturers due to the high price of raw materials and low seafood prices. New raw materials, changes in aquafeed recipes and the need for more efficient feed processing to reduce costs have been some of the demands to feed technology suppliers. Aquafeed.com talked with some of them to get their insights and how they see 2024.
Automation
In the current context, increased automation has been the one of main focus of feed mills. “The combination of economic pressures and a growing focus on sustainability has driven feed mills to actively pursue operational efficiencies across all aspects of production,” said Rob Strathman, president of Famsun-USA. “They are seeking advanced equipment and automation technology. We are busy transitioning extrusion from an art to a science and are using this data to create an automation system that streamlines the operation while delivering multiple benefits in waste reduction.”
“Several factors have contributed to the growing interest in plant automation, such as a substantial evolution in the variety and quantity of components required for aquafeed production and a heightened quality. This necessitates a more efficient and precise approach to the handling of micro components. Rising costs associated with micro components further emphasize the need for cost-effective and accurate dosing methods to minimize waste and expenses,” said Javier Solano, area sales manager LATAM at KSE Process Technology.
“Next to this, there is a shortage of manual labor in plants worldwide has made it increasingly challenging to rely on traditional manual dosing methods. A higher level of automation is the solution to this labor scarcity,” Solano said. “To meet these demands, we feature micro-dosing equipment capable of dosing quantities ranging from 50 grams to 150 kilograms, hereby effectively covering the entire spectrum of microdoses required in most aquafeed production plants.”
“Instrumentation and automation throughout the line help feed processors achieve high efficiency and optimize throughput. Automatic startup and shutdown of the extruder, for example, can be implemented to reduce waste during those phases,” said Hadrien Delemazure, process engineer and market manager, Clextral.
Efficiency
Increased efficiency is of utmost importance as well and sometimes, it does not need too much investment. “Many production lines are not operating as optimally as they could and even by simple means can be brought under control. This can be as simple as leaking compressed air lines, steam systems without condensation recovery, motors not running on VFDs, etc.,” said Peter Sønderskov, sales manager aqua feed and pet food at Process Integration. “We often spend time on-site helping create the full overview of the process and highlighting the potential for optimization of the plant without having to invest. Many times, the complete overview is overseen in the daily work and instead of just focusing on one piece of equipment, the running cost can be reduced once the total picture is in place.”
Sønderskov sees this tendency in shrimp feed mills. “Once capacity is limited, a new line is copied in parallel to the existing line(s) at the plant, before the plant is mapped, and the utilization of spare capacity is taken into use. If we compare with the salmon feed industry where the focus has been on automatization and efficient high-capacity lines, the shrimp feed industry is still in a learning phase and can be more efficient in terms of energy, up-time and OEE (overall-equipment-efficiency), in the end optimizing of the running cost and profitability of the feed manufacturing.”
Digital manufacturing is a prevalent trend cutting across all industries to increase efficiency. “One crucial advantage of embracing the concept of a digital factory lies in the heightened operational data it generates and its ability to shed light on areas of operational inefficiency. Already, several forward-thinking aquafeed companies have reaped substantial financial rewards from such operations and we are regularly learning of others kicking off new initiatives to reach this end. To maintain competitiveness, all manufacturers will need to integrate a digital strategy into their operations,” Strathman said.
“For all regions, elevating your production process to the next level can significantly enhance efficiency. This includes reducing maintenance requirements, optimizing the use of raw materials, minimizing manual labor, and improving product quality while reducing cross-contamination and enhancing ingredient traceability. Furthermore, reducing energy consumption or implementing smarter energy utilization practices should be considered,” Solano said.
Energy
Energy was one of the main issues in 2022 and continues to be in 2023. “The aquafeed production process is more complicated than terrestrial animals, so energy is always an important topic. Bühler has different services and is continuously developing new solutions that allow our customers to reduce energy consumption and significantly reduce the CO2 footprint until a CO2-neutral aqua plant is achieved. The solutions are not only available for new dryers but can also be retrofitted to existing systems,” said Chao Luan, head of Market Segment Aqua, Bühler (Changzhou) Machinery Co., Ltd.
“Given the challenges posed by inflationary pressures, the focus on energy efficiency remains a prevailing trend. It’s noteworthy that the drying operation in aquafeed production is the largest consumer of energy. In response, we have introduced a cutting-edge dryer control system designed to adapt the exhaust volume to align with the dryer’s evaporative load. This approach enables the dryer to function efficiently at varying production rates while maintaining optimal energy efficiency,” Strathman said.
With the increase in energy prices, dryer technology with an air recirculation system is another solution. "CPM introduced IDAH’s Carousel that lowers the energy use by 25-40% and reduces the amount of air emission by 30-50%, thus, it can decrease the odor problems typically found in aquafeed factories," said Danny Chang, CPM general manager.
Digital solutions are able to bring huge economic values to aquafeed producers by improving production efficiency and also saving energy costs. "In China, one aquafeed customer has achieved ~20% of energy saving by using our digital solutions,” Luan said.
“Not only do feed producers expect processing equipment to be energy efficient, but there are growing expectations for equipment to produce a variety of products without significant changeover costs. Therefore, there is an expectation of high volume capacity (to meet demand profitably) but an equal expectation for maximum flexibility of what is produced. This can be done, but it takes collaboration between producers and equipment suppliers,” said Jesse Mitchell, sales engineer, Wenger Aquatic Feed group.
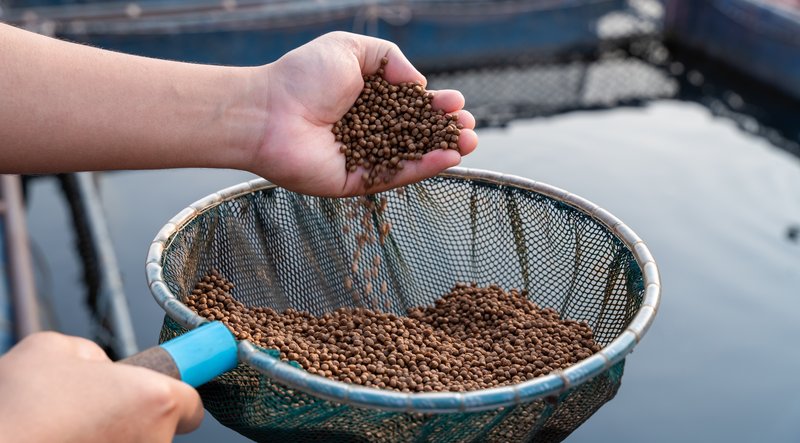
Credits: Shutterstock
Dealing with a diversified raw material basket case
Novel ingredients are being introduced in feed production to substitute the low availability of traditional raw materials and that has an impact on the manufacturing process. “The aquafeed industry is being challenged by fluctuating costs and availability of ingredients to produce a nutritious product, while at the same time seeing the sale price for feed decreasing. Feed producers are being forced to explore alternative ingredient sources, which can have a major impact on the production process including the efficiency of extrusion and drying,” said Mitchell.
“The current context has also increased the need for upgrades in relation to handling new raw materials and inclusion in different process steps as an opportunity for better utilizing the feed plant and thereby reducing the cost of feed due to smart engineering,” said Sønderskov.
“Recipes need to be modified and processing parameters changed. For example, we can see a need for a preconditioner with a longer residence time and higher mixing capacity. In this case, the flexibility of the twin screw extruder is key, as it can adapt to process a range of recipes from many raw materials and produce well-balanced and nutritional feeds,” said Delemazure.
“Some novel ingredients are likely to retain certain functional properties, particularly binding capabilities, making them a valuable asset to extrusion and pellet quality enhancement,” Strathman said.
More raw materials also translate to increased complexity in the storage and dosing of ingredients. “This raises the necessity for equipment that offers remarkable flexibility in formulations for feed mills. For instance, our movable weighers equipped with weigher-in-weigher concepts offer an extensive range of dosing possibilities that are unparalleled in the market,” Solano said. “Some raw materials may also pose flowability challenges, which is another area where extensive experience comes into play.”
“Global demand for shrimp and salmon is estimated to grow about 5% annually over the next decade. This means higher production of slow- and fast-sinking feeds. Producing nutritious sinking feed – especially in micro sizes – can be challenging, especially with changes in ingredients and formulations. Customers want systems that are flexible enough to adapt to changing inputs,” Mitchell said.
“To incorporate more plant-based ingredients in shrimp feed formulation, the use of high moisture pelleting and a combination of a dryer and cooler in the pellet mill enables sustainable and energy-efficient, consistent and high-quality shrimp feed pelleting that also saves on steam and raw material cost,” said Chang.
Requests for technologies that enable traceability of raw materials, production parameters, and quality control data have also increased. “This capability is increasingly important for transparency and product differentiation. It is also crucial to ensure feed safety compliance with industry standards and regulations, boosting consumer and market trust,” Strathman said.
New projects
The aquafeed industry has been suffering from high raw material prices and a lower feed demand from farmers. Has this scenario affected new projects? The answer is yes but for a short term.
“Raw materials are an important part of the feed cost (up to 90%). Price increases or low availability of those raw materials can certainly have an impact on projects,” said Delemazure.
“Nevertheless, the aquaculture industry, on the whole, remains on a promising growth trajectory, and we anticipate a natural resurgence in the feed sector's expansion in the near future,” said Strathman.
“In the Norwegian salmon market, larger projects have been put on hold and the focus has been on upgrading and utilization of spare capacity in existing production facilities. This involves more engineering work and survival than normal, which for us means high activities,” said Sønderskov.
“Regions such as Eastern Europe, Asia, Africa and the Middle East were not affected. We are seeing high demand for sturgeon, trout, salmon and shrimp,” said Delemazure.
“Following our visit to Aqua Expo in Guayaquil (Ecuador), it was evident that the shrimp market is showing a noticeably more positive atmosphere, despite the drop in shrimp prices. Interested parties were all willing to discuss new projects and production line upgrades, which strongly reinforces the perception that the shrimp production sector, unlike fish species, continues to experience growth and maintains a positive outlook,” Solano said.
What to expect in 2024?
“Barring the possibility of major external disruptions, like conflicts in the Middle East, our outlook for 2024 is positive. We acknowledge that our customers will grapple with ongoing high inflation, which will impact their purchasing choices. Nonetheless, we are strategically positioned to support our customers in identifying and implementing additional operational cost-saving measures,” Strathman said.
“2024 looks like the trends are very much on sustainability, energy consumption and a change towards green energy sources. This transition to green energy is not a quick fix and will be in focus for the coming years. As green technology is moving fast at the moment, we’ll see costs coming down and getting more attractive to many users. The industry is moving slowly in the right direction and will for sure take off, as the cost of technology is coming down,” said Sønderskov.
“In the context of aquaculture systems, the production of feed remains one of the most environmentally impactful aspects. Our strategy for 2024 involves partnering with key industry players to provide cutting-edge equipment and innovative solutions to significantly reduce the environmental footprint associated with feed production,” Solano said.
“Our aquafeed customers have a positive outlook for 2024, with the hope that ingredient supply constraints will return to normal and feed pricing will stabilize. There is no doubt that global demand for certain species is increasing. The key is being able to produce higher volumes of certain feeds, with proper nutritional aspects and consistent quality, in a profitable manner. To do this, the processing equipment should be designed and set up specifically for aquafeed production,” Mitchell concluded.