ANDRITZ Feed & Biofuel introduced a comprehensive portfolio of Automation and Digitalization solutions for the feed industry under its Metris digital platform at Victam Asia. This continuously evolving, universally compatible platform supports operational efficiency, resilience, readiness and sustainability, and aims to allow for fully autonomous feed plant operations by 2027. Aquafeed.com talked with the ANDRITZ team to get insight into these new solutions.
Bringing proven technology from other industries
ANDRITZ Group operates in different industries, such as the pulp, paper, mining, and hydropower industries, among others, and is now bringing the technology that has been applied to those industries to the feed industry. “The pulp & paper industry is ten times more complex than the feed industry with 24/7 operation. The same happens with hydropower plants. Our solutions, developed in the past 20 years, have allowed the digitalization of these industries. Most hydropower plants are now completely autonomous, running 24/7,” Michael Lierau, Senior Vice President at ANDRITZ Feed & Biofuel, explained.
“The feed industry is behind in digitalization and needs partners that have gone through this journey, that have the infrastructure, the platform, the hardware, and software, and that's something that ANDRITZ can step in. We did the transition in pulp, mining, and hydropower industries to the fully digital and automated plants, and this is what we want to do for the feed industry, to be that partner that builds that roadmap, step by step, and takes them towards this journey,” Dr. Sohail Nazari, Vice President and Head of Automation & Digitalization, ANDRITZ Feed & Biofuel, said.
Applications
The Metris platform gets data from each part of the feed mill through the installation of software, sensors, and tools that ANDRITZ has developed internally which allow real-time monitoring of the whole production process. With this data, ANDRITZ is able to bring different applications to process optimization, asset management and capacity building.
One of the new concepts in the feed industry is Risk-based management, which allows the operator to detect the risks and fix them. “What we do is we take all data from the different tools and applications, we aggregate them, and we build an integrated risk-score. For example, the pellet press has a high risk and the customer can go deeper and find where the risks come from, for example, from motors. The app is able to identify from which motor the risk is coming and that can make decisions very quickly,” Nazari explained. “We are coming from a top-down approach. We're taking a look at what is your highest risk and why it is coming from it.”
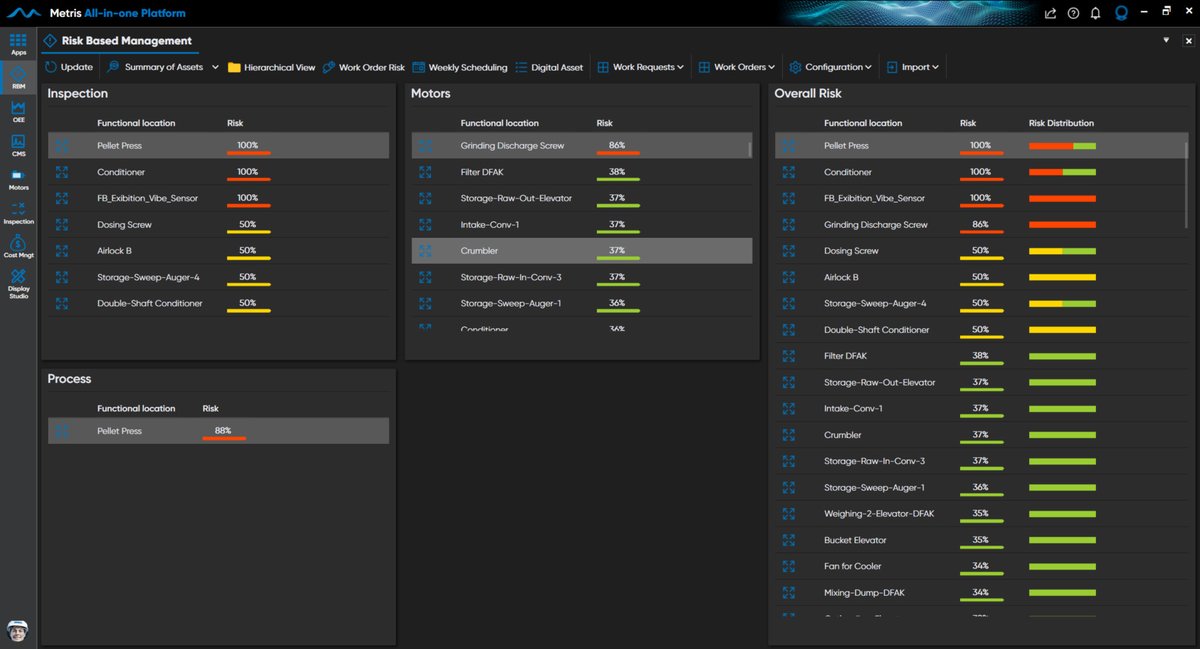
Moreover, the system goes beyond sensors and allows for documenting other issues and tracking them. With all this information, everybody will know what is working and what is not working. “If somebody finds an oil leak, the platform immediately adds it and recalculates the overall risk. It cascades and then your risk score goes up. So, staff know that they have to react to it. That is the strength of this platform, we are pulling in data from every different direction, aggregating it, and making it easy to digest this information,” Nazari explained.
“All this is predefined and customized. The time it takes for any feed mill to deploy this type of software is very quick. That is where we bring our process know-how combined with our technology,” Nazari said.
“We are getting to a stage where there is not that much you can do anymore. Physics is physics, and sometimes, there is little you can do there. We are helping operators to better use the machine by getting a more transparent view of the process with a control system,” said Lierau.
Risk-based management is only one of Metris' solutions. Control systems can also help with one of the current key issues in the industry: energy consumption. “With patented advanced process control technology, we are able to decrease the energy consumption in equipment like dryers or coolers while pushing for more production and achieving better quality,” Nazari said.
“Process control can also help, especially big players, by setting up a remote center of excellence. Instead of having operators living in places that require travel, remote centers of operation can help reduce the carbon footprint,” Nazari said.
“We still use our processes in a very crude manner, and we have to look into areas that we never think about. For example, manufacturers look at the dryer as a high-energy consumer but do not think about how they can reduce the amount of air that is pushed into the system. Metris can monitor all of this easily, creating sensitivity for the plant owner. As process engineers, we provide an enhanced solution,” Lierau said.
The process simulator
Another solution that the platform brings is the process simulator. “We can build the model of the plant that can mimic the operation characteristics with 5% accuracy. The solution is dynamic, so you can see, second by second, how the operation works. Moreover, we can model the particle size distribution, the quality, the amount of moisture inside the pellets and all energy consumption,” Nazari explained.
The simulator can also be applied to greenfield projects to make sure they are designed correctly. “It allows you to make sure the valves, the pumps, the equipment, the pipes, the conveyor system, the elevators, etc., are all correctly designed. Another application is that we can use this model before real plant commissioning. We commission the system 'virtually' three months in advance and find all the problems that would have occurred during real commissioning three months later and solve them in advance, so that the real commissioning is drastically shorter than without this virtual step in advance,” Nazari said.
Moreover, ANDRITZ built a training simulator for operators. It can be used in greenfield projects training operators months in advance before the plant starts up so that they can learn how to operate it, decreasing the wrap-up time. “On brownfield projects and operating plants, we can build an operator training simulator with the same concept that the airlines build the flight simulator. We can train them remotely and that helps with environmental commitments. It is a proven fact from the military and airline simulators that operators using training simulators learn how to operate a plant four times faster than with traditional training,” Nazari said.
The models are built based, on the one hand, on the physics of feed processing and how the equipment should work, and, on the other hand, on live data inputs from the feed manufacturer. “Feed mills can provide this data which can be put into the model, or we can provide the model, train them, and our customers can do it themselves. The simulator is a combination of data and physics,” Lierau said.
Protecting feed operations from cyber risks is crucial, and ANDRITZ owns its own cybersecurity company to ensure the highest level of security standards. “We did that to work with hydropower plants. We have the highest IEC cybersecurity standard,” Lierau said.
Industry adoption
The feedback from the feed industry so far has been very positive. “It is something that people have been longing for quite a long time, but now they suddenly see it. We didn’t come up with a concept where we first need to bring a reference. ANDRITZ already has hundreds of references all over the globe from the pulp, paper, and hydropower industries,” said Lierau.
The company has around 2,200 people dedicated to plant automation. "Based on more than 35 years of global experience in machine and plant control systems, ANDRITZ is the ideal partner in Automation & Digitalization for the realization of complex control systems in the entire industrial environment. I believe Metris will have a more radical impact on the industry that most people actually see,” Lierau said.
And how different is adopting new technologies in different markets and players? “You would be surprised that developing countries are much more accepting of change than Western countries. This is something that, from my career of bringing automation and digitalization into process industries, originally shocked me, and I can see it in all the different industries. Since developing countries have to catch up, the only way is through technology,” Nazari said.
The same happens when it comes to small and big players. “The only way to have the same efficiency as the big players is to use digital technologies. Metris is a top-tier solution, even the small feed millers out in Africa can afford the solution because we can strip it down to essentials. It is not something limited to just one group of customers,” Lierau said.
“Bigger players have other opportunities, such as consolidating the operation in different plants, remote operations, building a central remote operation, etc. These are the problems that the bigger operators are facing, with plants around the world all running differently. This is not a problem just for the feed industry, it is also for the pulp, mining and hydropower and the interesting part is that all the other industries have solved them already, but the feed industry has not even started,” Nazari said.
ANDRITZ is extending these technologies beyond its own equipment to encompass the entire plant, even in cases where ANDRITZ's equipment is not installed. “In the mining industry, we don't have the equipment, but we have helped them to go through the whole process landscape and improved their operation drastically,” Nazari explained.
“Ten years ago, this was a dream, but today, we are talking about reality, all because ANDRITZ Group invested tens of millions of dollars to develop all this. If we were only a feed equipment provider, we would not be able to do that. We are offering these models unheard of in the animal feed industry,” Lierau said.
“ANDRITZ was in the 80s the first player bringing automated solutions to the industry. Now we are bringing automation and digitalization solutions to entire plants. The time for change has come for the feed industry, and ANDRITZ will be the pioneer of that change because we never stand still,” Lierau concluded.