Since 1974, Taiwan-based IDAH has been developing innovative products for the aquafeed, food, pet food and biomass markets. When IDAH joined CPM in 2023, they gained access to a range of collaborative opportunities, expertise and tools that they could use in developing their own products.
This week, IDAH launched the clearest evidence of that collaboration yet at VICTAM Asia 2024 exhibition: the all-new TwinTech Twin Screw Co-Rotating Extruder.
The innovative extruder updates IDAH’s industry-leading twin-screw extruder with innovations and design techniques from Ruiya Extrusion, along with a long-lasting gearbox and energy-efficient motor from CPM Industrial Solutions.
Collaborative development
“This extruder is a collaboration between IDAH and Ruiya,” said Albert Wang, assistant sales manager at IDAH. “We combined their insights on design and cost efficiency with our knowledge in feed production to introduce a new technology.”
CPM Industrial Solutions’ gearbox and motor also offer real-world benefits in TwinTech. “The gearbox allows rotational speeds up to 600 RPM, facilitating heavy-duty processing and increased output, along with a proven long-life track record,” said Wang.
The TwinTech’s motor from CPM Industrial Solutions is a permanent magnet synchronous motor (PMSM) that offers significant advantages. “The CPM motor has lower energy requirements,” said Wang. “It also has a reduced size, and reduces noise output by about 30%.”
Combined, these innovations create a market-leading twin-screw extruder that delivers capability, value and reliability.
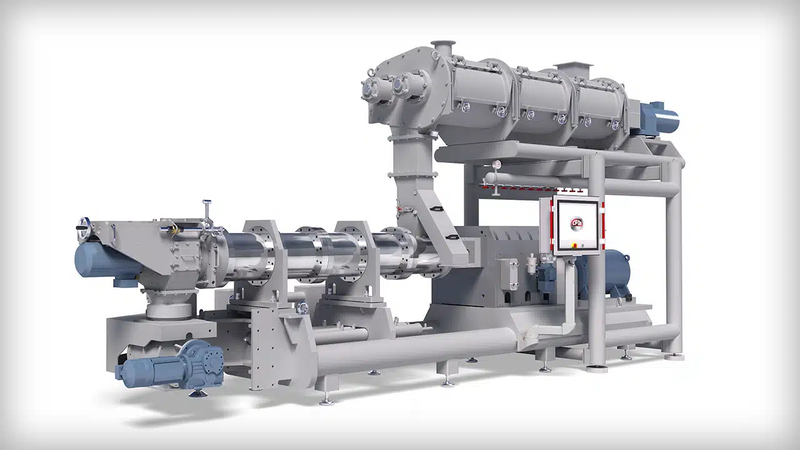
TwinTech features
The TwinTech extruder offers a range of new features developed by both IDAH and partner brands within CPM.
Enhanced Gearbox Technology: Powered by CPM’s field-tested gearbox technology, the TwinTech extruder features a high-speed, heavy-duty gearbox capable of achieving rotational speeds of up to 600 RPM. This allows for increased processing capacity and efficiency.
Energy-efficient design: The TwinTech extruder is powered by a permanent magnet synchronous motor (PMSM), which is highly efficient and about 50% smaller than traditional air-cooled motors. This motor design contributes to energy savings, reduced noise pollution (up to 30% lower) and the option for water cooling to maintain motor efficiency and stability.
Density control unit: An optional feature, the density control unit, allows TwinTech to produce different types of fish feed, including sinking and slow-sinking feeds, by using positive pressure inside the cutter chamber. This versatility allows manufacturers to produce a wide range of fish feed with a single machine.
Advanced preconditioning and cooking systems: The TwinTech extruder introduces a new thermal hydrator and updates the differential diameter conditioner to improve the hydration and retention time of materials. These systems are designed to enhance the cooking process by ensuring efficient steam integration and retention, leading to better processing efficiency and product quality.